About us
- Home
- About us
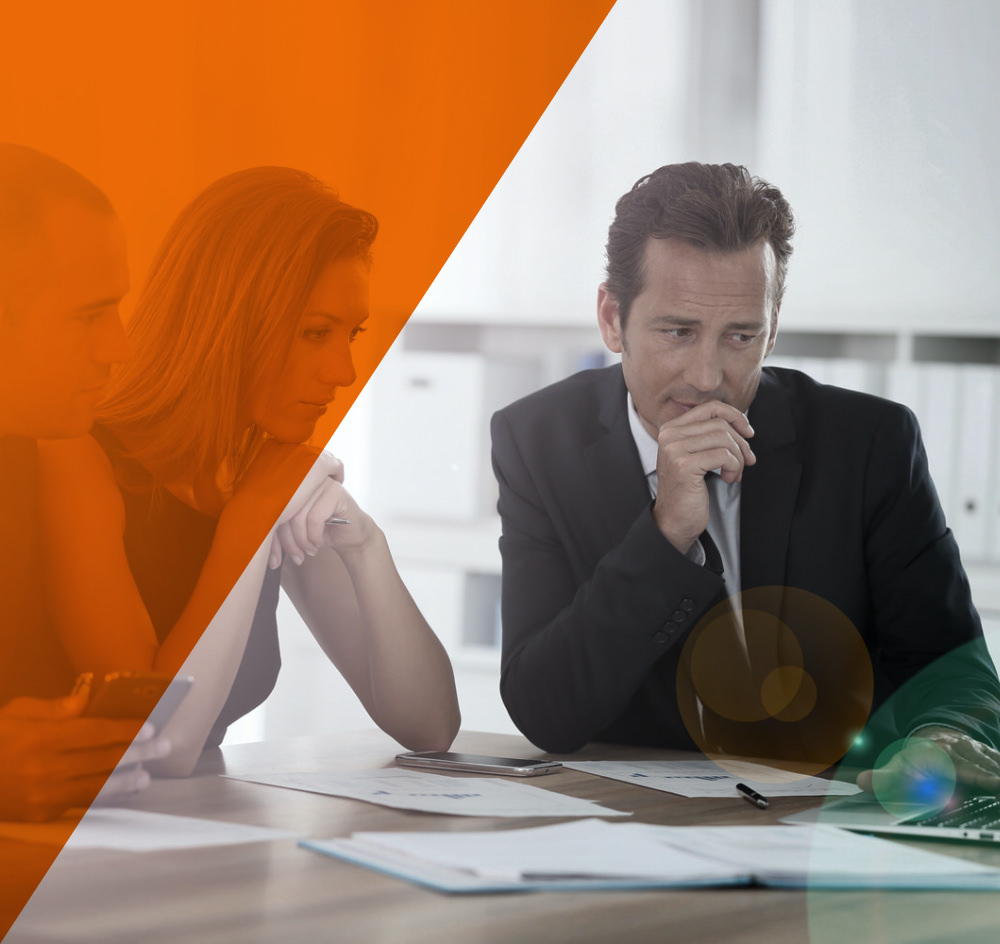
The ITRack Brand
Since 40 years we have specialized in production of 19" Rack Cabinets for the electronics, electrical engineering, telecommunications and data transmission sectors, with special focus on enclosures for active network equipment, passive components for structured cabling and servers for IT infrastructure.
Our products are ideally suited for installations both in small and large enterprise environments, backbone & network cabling, Data Center, Edge Data Center, Micro Data Center, industrial production environments, and for securing video surveillance equipment.
MADE IN ITALY
Brand not affected by geo-political issues
CORPORATE SOCIAL RESPONSIBILITY
ITRack donates a percentage of its profits to fund social solidarity actions
EXTENSIVE PRODUCT RANGE
19” rack cabinets and accessories for every technology need
INTERNATIONAL DISTRIBUTION NETWORK
Worldwide distribution network
Design & Project Engineering
Project engineering and design are made using the most up-to-date digital tools, utilized by our expert operators who are constantly keeping their skills up to date. Two CAD stations are operating in our design and engineering department and are capable to process a very high number of part numbers in record time.
Production process
ITRack has automated all stages of manufacturing and eliminated the need to resort to external suppliers. As a matter of fact, constant investments in specialized personnel and technologically advanced machinery, ensure that the company can guarantee industrial production with certain times and at maximum quality, while in comparison to the market, it can achieve customized production at extremely competitive time and cost.
The TRUMPF 5030 FIBER and TRUMPF L 2510 Laser Cutting Systems are compact and flexible workstations. They are completely automated since they are equipped with automatic loading and unloading mechanisms.
Bending operations are performed with bending presses of the latest generation; through angular laser control function, they can realize folding from the simplest metal component to the most complex one.
The operating cycle of the equipment is fully automated and includes loading, bending, and unloading stages. Flexible and modular solutions for unattended material management and operation, are improving productivity, efficiency, and quality.
We use a powder coating plant with four newly designed cabins that are equipped with suction system and manual retouching stations fit out to change colour safely in a record time of 12' minutes. With phosphate treatment and degreasing, the outcome is better adhesion of powder paint thus attaining very high level of surface resistance against corrosion.
The company uses a powder coating system with 4 new-concept booths, each equipped with an extraction system and manual retouching stations, in which colors can be changed safely in the record time of 12 minutes. The degreasing and phosphating tunnel guarantees effective powder adhesion to any surface, which maximizes corrosion resistance.
Our proprietary verification system allows real-time monitoring of the work of each one of the operators and of every single machine. The semi-finished parts are reaching Quality Control, practically perfect. The verification system detects, collects, and processes productivity data with the aim of attaining high productivity levels, excellence in production and constant increase of competitiveness.